Written by Sabre Plastics Tooling in Collaboration with Rinco Ultrasonics
When it comes to creating a secure and lasting bond between a brass insert and a plastic component, two main techniques come into play: ultrasonic welding and heat staking. Both methods offer advantages, but ultrasonic welding stands out for its efficiency, strength, and versatility. Let’s delve into the specifics of ultrasonic welding brass inserts and how it surpasses heat staking in several key areas.
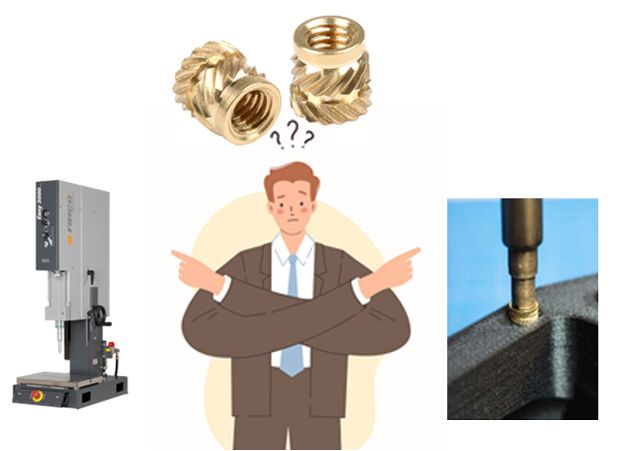
The Power of Rinco Ultrasonic Welding: How Ultrasonic Welding Works
Ultrasonic welding utilises high-frequency vibrations to generate localised frictional heat at the interface between the brass insert and the plastic part. Here’s a breakdown of the process:
- Precise Positioning: The pre-formed brass insert is placed in a slightly undersized hole in the plastic component.
- Ultrasonic Activation: An Ultrasonic horn / sonotrode comes into contact with the insert.
- Frictional Heat Generation: The vibrations of the horn cause friction between the insert and the plastic, generating heat.
- Plastic Melting and Bonding: The localised heat melts the plastic surrounding the insert, creating a strong mechanical bond as the melted plastic cools and solidifies.
The entire process is precise, clean, and generates minimal thermal stress on the surrounding plastic.
Staking its Claim: Understanding Heat Staking
Heat staking, on the other hand, relies on direct heat application to melt the plastic around the insert. This can be achieved through various methods, including heated tools or thermal elements. While effective, heat staking presents some limitations:
- Risk of Heat Damage: Excessive heat can degrade the surrounding plastic, leading to warping or reduced strength.
- Uneven Heating: It can be challenging to achieve consistent heating throughout the interface, potentially compromising the bond strength.
- Slower Cycle Times: Heat staking often requires a longer dwell time to allow for proper plastic melting and cooling, impacting production speed.
Ultrasonic Welding: A Clear Winner
Ultrasonic welding offers several advantages overheat staking when it comes to inserting brass into plastics:
- Stronger Bonds: The frictional heat generation creates a more robust mechanical bond between the insert and the plastic compared to heat staking.
- Faster Cycle Times: The rapid heating and cooling process of ultrasonic welding translates to faster production cycles. Typically Heat Welding takes 5 seconds per cycle time and Ultrasonic Welding is 90% quicker at roughly 0.5 seconds.
- Reduced Thermal Stress: Localised heat generation minimises the risk of thermal damage to the surrounding plastic.
- Clean and Precise: Ultrasonic welding offers a cleaner process with minimal heat distortion or flashing.
- Energy Consumption: Heat welders need to maintain heat constantly throughout operation, leading to higher energy use. Ultrasonic welders only require energy during the short welding activation period, making them more energy efficient.
Applications For Insert Staking:
Brass Insert Welding finds application in various industries due to its strong and reliable bonds. Here are some prime examples:
- Automotive: For embedding threaded inserts into plastic components for dashboards, consoles, and door panels.
- Electronics: Securing brass grounding points and threaded inserts in electronic housings.
- Consumer Goods: Creating strong attachment points for handles, hinges, and other hardware on plastic parts.
- Medical Devices: For secure integration of brass inserts into medical equipment housings.
Overall, ultrasonic welding offers a superior method for inserting brass inserts into plastics. Its speed, precision, and ability to create strong, reliable bonds make it the preferred choice for a wide range of applications.
Contact us today to discover how Sabre Plastics Tooling Ltd can find the best solution for your production needs – www.sabreplas.com